Manufacturing and Customisations
Aussie Buckets strives to raise industry standards of quality and excellence in all areas of manufacturing. Our partners' extensive experience, industry recognition, and vast production capacities allow us to meet and exceed customer expectations, delivering exceptional attachments that stand the test of time.
Key Stats
11
Global Manufacturing Locations
7,450
Attachments Annually
10
Rigorous Inspection Points
97
Customer Satisfaction
4
Of Revenue Spent On R&D
30
Steel Grades Available
Our Certifications
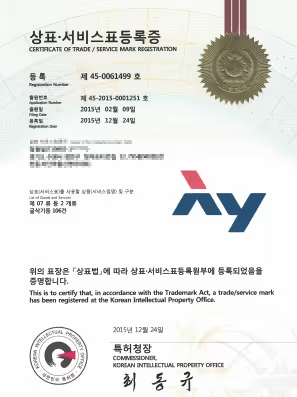
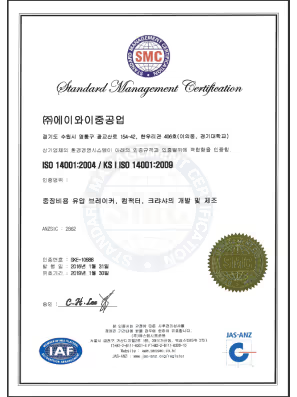
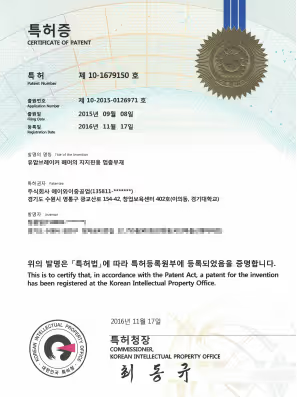
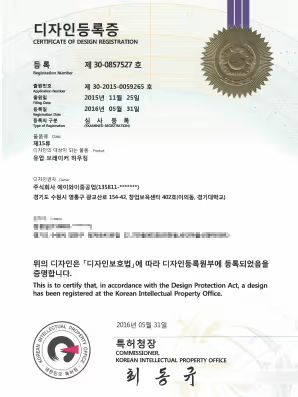
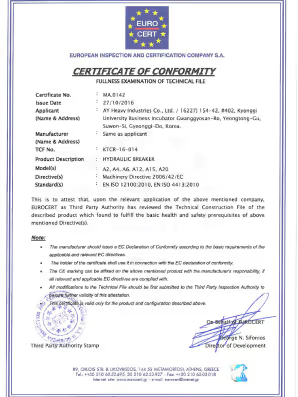
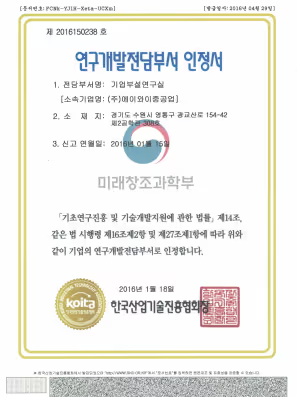
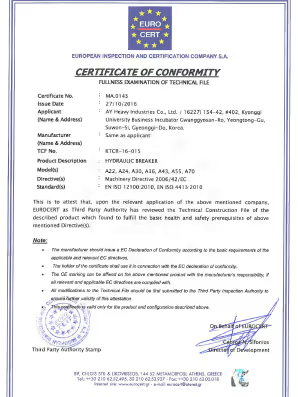
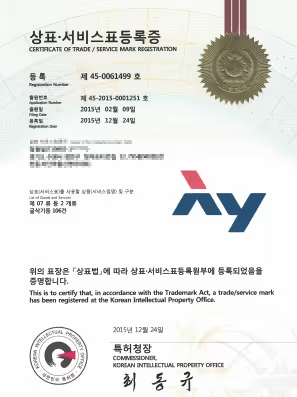
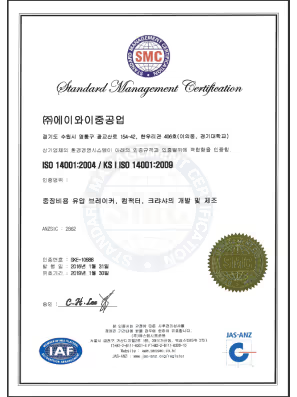
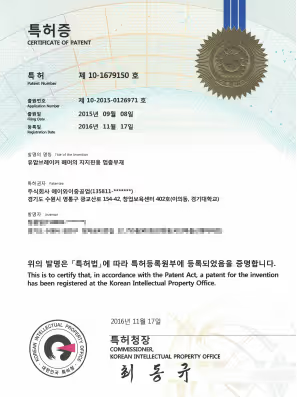
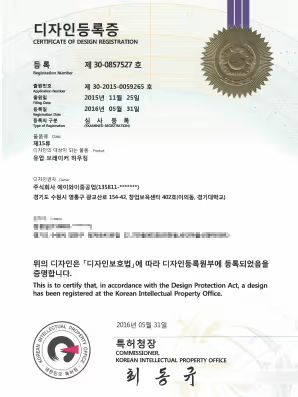
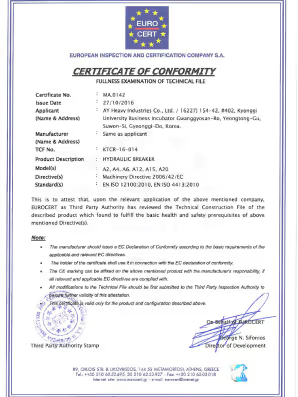
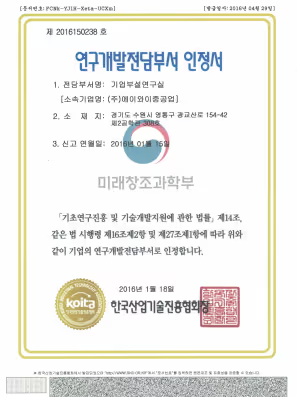
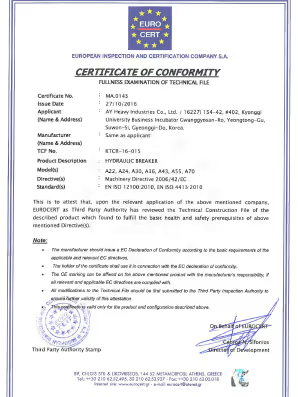
Customisation Options
All products are 100% purpose-built and customisable, giving customers greater customisation options and improving performance.

























* To confirm exact customisation options, speak with your attachment specialist. Specialised products may have certain customisation limitations due to design.
Order Process
See what to expect from your order process, including a breakdown of how long each stage generally takes.
Manufacturing Begins - Day 1
Order details are confirmed with the manufacturing team and production starts immediately.
Manufacturing Completion - 2 - 4 Weeks
You will receive email notifications throughout each stage of manufacturing.
Shipment - 4 Weeks
You will receive email notifications for: Departure Notice & ETA, Initial Balance Request and Arrival Notice.
Processing & Delivery - 2 - 7 Days
Your order is processed for site delivery, local pickup or depot delivery.
Order Complete
Pickup of delivery has been accepted and your order is ready to be attached to your machine.
Order Follow Up
Our team will follow up with you 14 days after delivery or pickup to ensure everything is running smoothly.
Case Study
Wayne needed a solution for cutting sandstone in a more efficient manner than conventional single-blade rock saws. He was previously using a belt drive saw, which frequently broke down and cost him a lot in repairs whilst struggling to find customisation in other rock saw suppliers on the market.
After several iterations, our design technicians delivered to Wayne a 3-blade saw with 500mm spacing between each blade, with the option to detach the middle blade for added versatility.
Post delivery and after a quick break-in period, Wayne noted that his production on-site had doubled with the increased efficiency due to his new custom equipment.
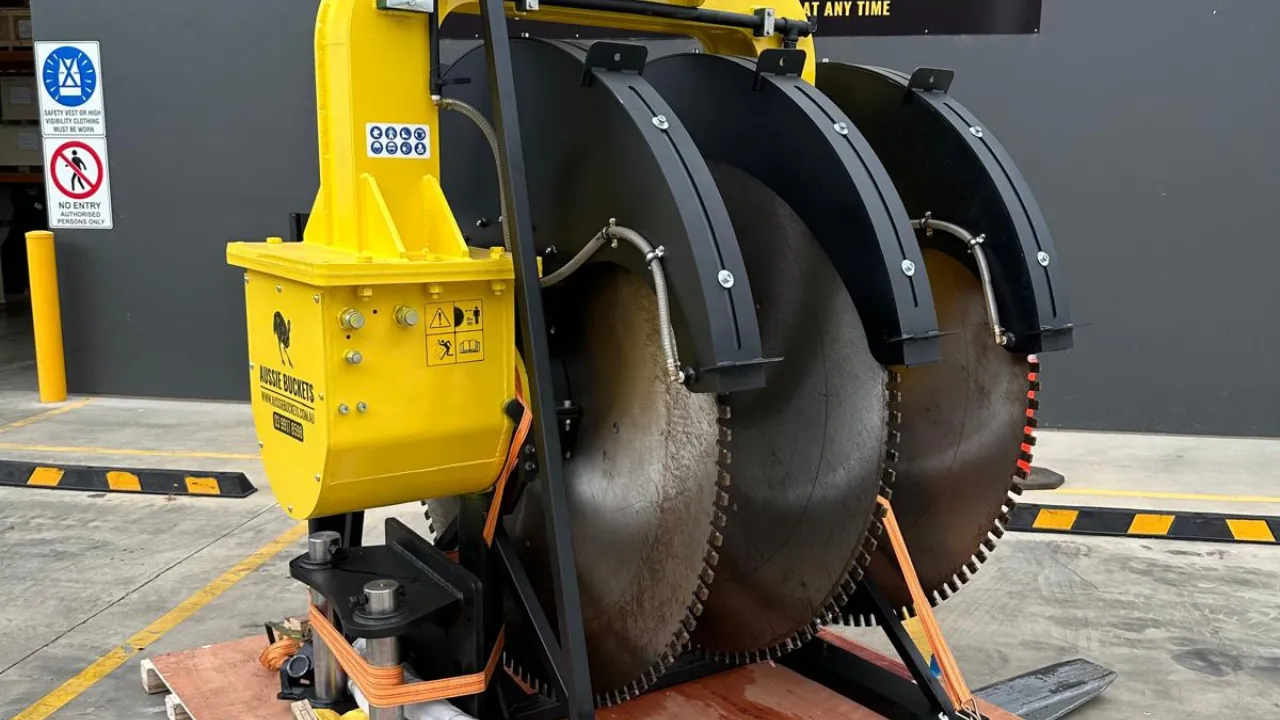
CONTEXT
Wayne needed a solution for cutting sandstone. He was previously using a belt drive saw, which frequently broke down and cost him a lot in repairs. Additionally, he struggled to get responses from other Rock Saw suppliers. Wayne's goal was to achieve efficiency comparable to his competition.
RESPONSE
Our technicians initially approached this request with designing a 2-blade saw with options for 500mm and 1000mm spacing between blades. After further discussions, we evolved this to a 3-blade saw with 500mm spacing between each blade, with the option to detach the middle blade for versatility. The final design allowed for multi-functionality: 3 blades cutting 500mm wide blocks or 2 blades cutting 1000mm wide blocks.Multiple design iterations were required to ensure desired functionality and efficiency of which was overcome through trial and error, along with continuous confirmation andminor adjustments along the way.
RESULTS
The final saw design met Wayne's needs and provided the desired efficiency. Despite initial issues with guard design, the saw performed well after adjustments.
Wayne initially faced a couple issues with the guards, which were resolved with minor modifications and noted a slight drop in production, getting used to a multi-blade configuration for the first time. After a quick break-in period and adjusting flow rates, Wayne noted that his production on-site had doubled from before, with the ability to make multiple cuts in the same time-frame.
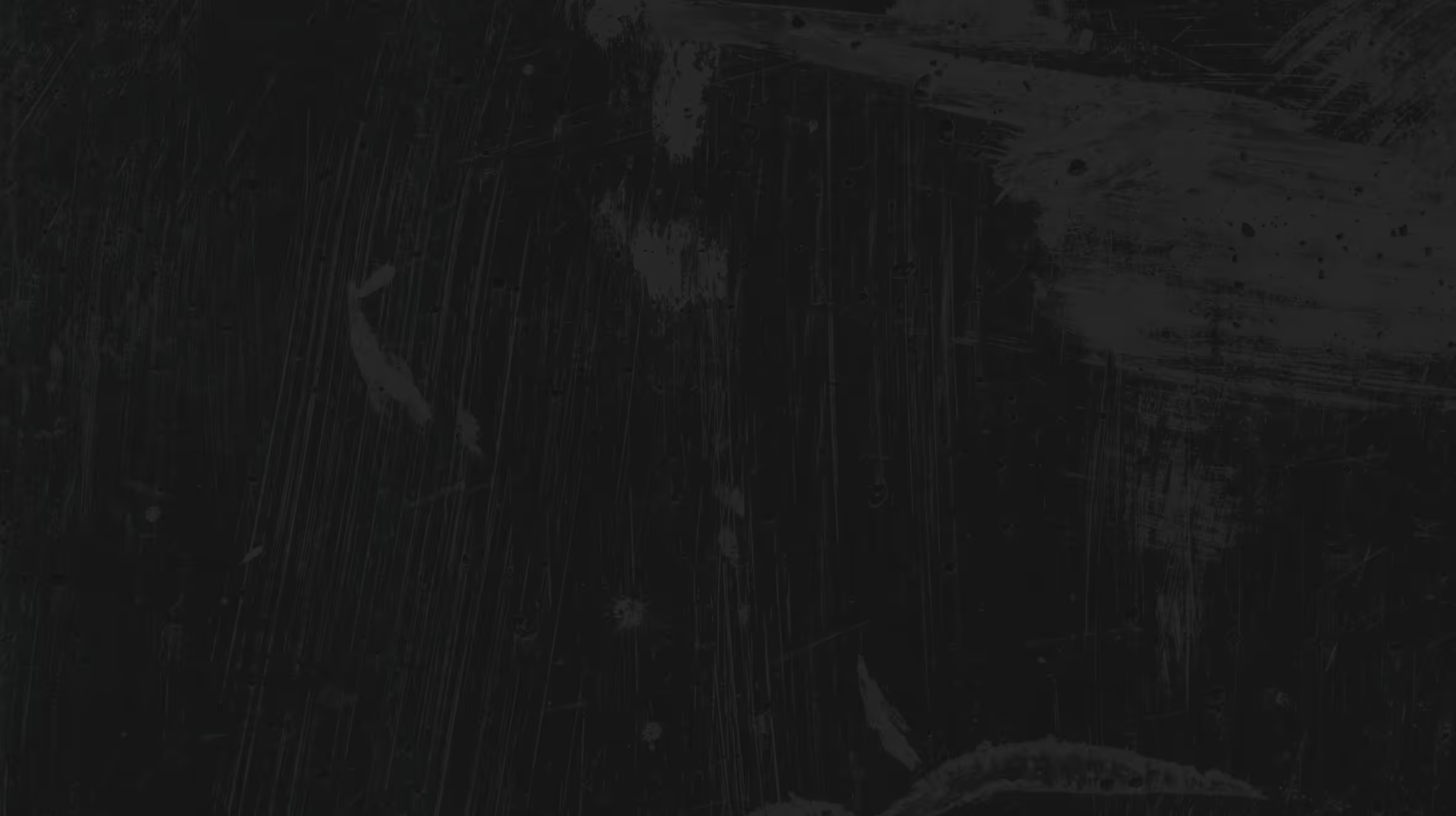
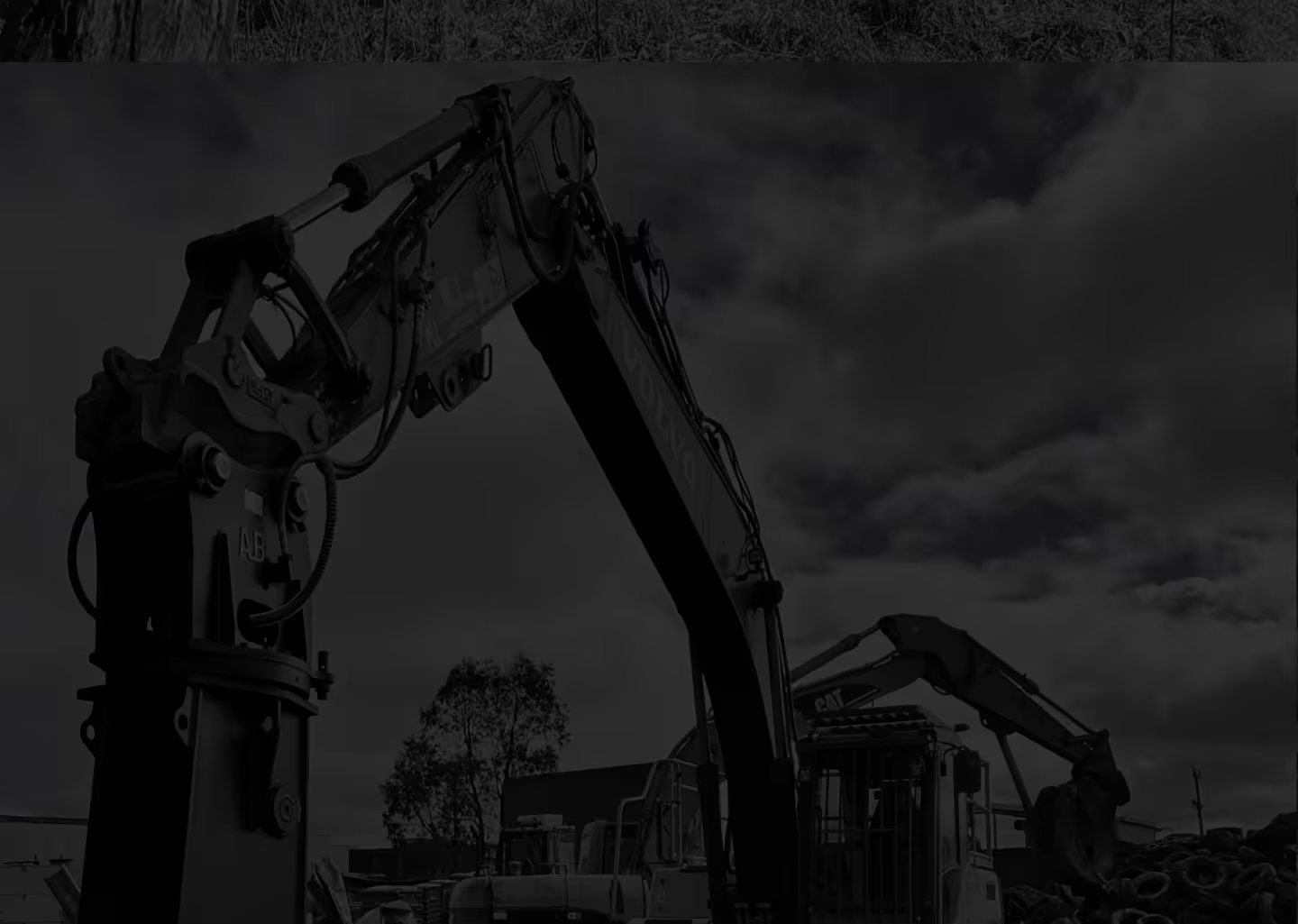
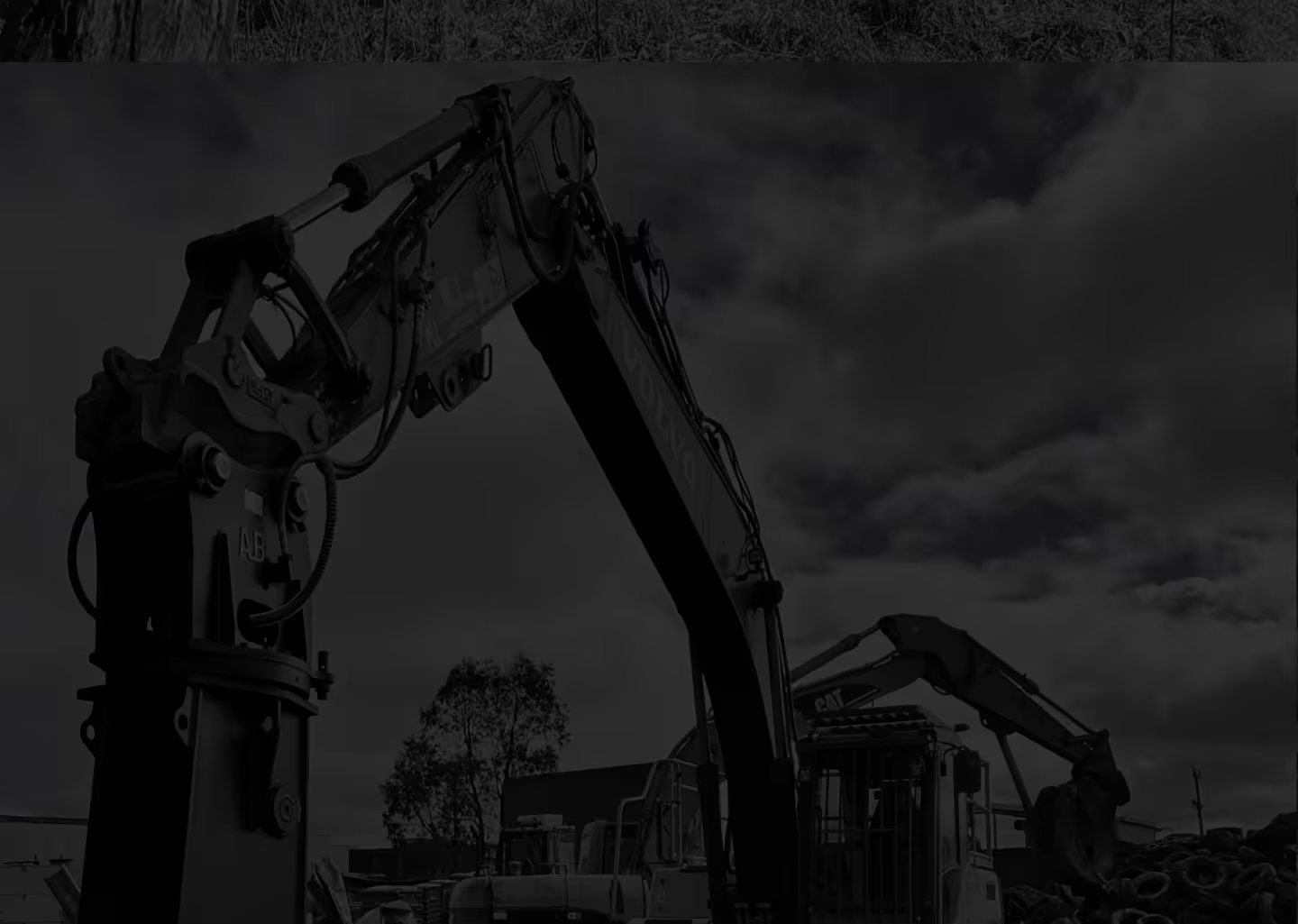